Cutting out the flanges for the water outlet manifold on a BCA mill modified to CNC.Cutter is 1.5mm.four flute carbide running at approximately 10,000 rpm with a feed rate of 100mm per minute.The nozzle is compressed air to keep the cutter free of chips.
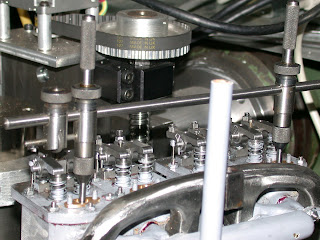
This image shows a trammel being used to measure the precise location of each of the water outlets from each cylinder
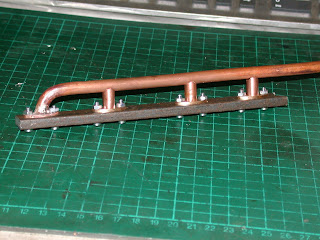
A strip of mild steel was jig drilled to duplicate the position of each outlet of the cylinders and the holes of the studs.This was the jig used to hold all the components of the manifold for silver soldering.
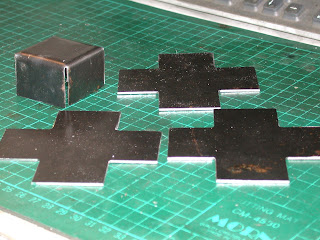
This is the modified ubolt bender used to bend the 8mm copper tube.
These shapes were made to form the tappet covers.
The cowling for the radiator was formed by two components, a flat sheet and a rolled strip.The flat plate had a hole cut in the centre then 12 flolds to form the shape.The ring was silver soldered in position Heat shrinking was required to reduce the outside of the cowling to fit the radiator
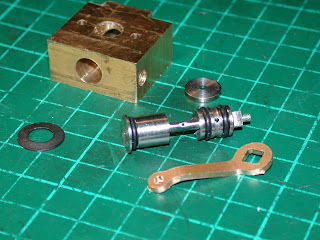
These two images show the model as at 16 -9-12
I plan to take the model to the 100th rally at Lake Goldsmith in November this year.
.
This is the body,and butterfly for the throttle. The main jet is 0.8mm drilled in the butterfly and fuel enters this jet through a hole between the two o rings.This component is made from 303 stainless.